Revision as of 20:18, 22 July 2006 editWBardwin (talk | contribs)Pending changes reviewers, Rollbackers20,628 edits Distinguish variant section← Previous edit | Latest revision as of 14:32, 30 June 2024 edit undoAszx5000 (talk | contribs)Autopatrolled, Extended confirmed users, New page reviewers28,045 edits Importing Wikidata short description: "Ancient type of pottery kiln"Tag: Shortdesc helper | ||
(95 intermediate revisions by 57 users not shown) | |||
Line 1: | Line 1: | ||
{{Short description|Ancient type of pottery kiln}} | |||
⚫ | [[ |
||
{{DISPLAYTITLE:''Anagama'' kiln}} | |||
1 Door about 75cm wide<br /> | |||
⚫ | [[File:Anagama kiln.svg|thumb|250px|right|Schematic drawing of an ''Anagama'' kiln:<br /> 1 Door about {{convert|75|cm}} wide<br /> | ||
2 Firebox.<br /> | |||
3 Stacking floor made of silica sand |
2 Firebox<br /> | ||
3 Stacking floor made of silica sand<br /> | |||
4 Dampers |
4 Dampers<br /> | ||
5 Flue |
5 Flue<br /> | ||
6 Chimney |
6 Chimney<br /> | ||
7 Refractory arch]] | 7 Refractory arch]] | ||
], Aichi]] | |||
The '''Anagama kiln''' is an ancient type of ] kiln brought to ] from ] via ] in the 5th century. | |||
] | |||
]]] | |||
] | |||
The '''''anagama''''' '''kiln''' (Japanese Kanji: 穴窯/ Hiragana: あながま) is an ancient type of ] ] brought to ] from ] via ] in the 5th century. It is a version of the climbing ] of south China, whose further development was also copied, for example in breaking up the firing space into a series of chambers in the '']'' kiln. | |||
⚫ | An anagama (a Japanese term meaning "cave ]") consists of a firing chamber with a firebox at one end and a flue at the other |
||
]; one of the largest of its kind in ]]] | |||
⚫ | An ''anagama'' (a Japanese term meaning "cave ]") consists of a firing chamber with a firebox at one end and a flue at the other. Although the term "firebox" is used to describe the space for the fire, there is no physical structure separating the stoking space from the pottery space. The term ''anagama'' describes single-chamber kilns built in a sloping tunnel shape. In fact, ancient kilns were sometimes built by digging tunnels into banks of clay. | ||
The anagama is fueled with firewood, in contrast to electric or gas-fueled kilns used by most contemporary ]s. A large amount of fuel is needed for firing, with stoking occurring round-the-clock until an appropriate temperature is reached. (Wood thrown into the hot kiln is consumed very rapidly.) ] and ] pieces will typically mature at "cone 10", a measure of "heat work" dependent on the final temperature coupled with the time required to achieve that temperature (see ]). Somewhat inaccurately, cone 10 could be thought of as a temperature range as high as 2375 °F (1300 °C). | |||
] | |||
The anagama is fueled with firewood, in contrast to the electric or gas-fueled kilns commonly used by most modern ]. A continuous supply of fuel is needed for firing, as wood thrown into the hot kiln is consumed very rapidly. Stoking occurs round the clock until a variety of variables are achieved including the way the fired pots look inside the kiln, the temperatures reached and sustained, the amount of ash applied, the wetness of the walls and the pots, etc. | |||
⚫ | Burning wood not only produces heat |
||
⚫ | Burning wood not only produces heat of up to 1400°C (2,500 °F), it also produces ] and volatile salts. Wood ash settles on the pieces during the firing, and the complex interaction between flame, ash, and the minerals of the clay body forms a natural ash glaze. This glaze may show great variation in color, texture, and thickness, ranging from smooth and glossy to rough and sharp. The placement of pieces within the kiln distinctly affects the pottery's appearance, as pieces closer to the firebox may receive heavy coats of ash, or even be immersed in embers, while others deeper in the kiln may only be softly touched by ash effects. Other factors that depend on positioning include temperature and ]. Besides location in the kiln, (as with other fuel-fired updraft kilns) the way pieces are placed near each other affects the flame path, and, thus, the appearance of pieces within localized zones of the kiln can vary as well. It is said that loading an anagama kiln is the most difficult part of the firing. The potter must imagine the flame path as it rushes through the kiln, and use this sense to 'paint the pieces with fire'. | ||
⚫ | The length of the firing depends on the volume of the kiln |
||
⚫ | The length of the firing depends on the volume of the kiln and may take anywhere from 48 hours to 12 or more days. The kiln generally takes the same amount of time to cool down. Records of historic firings in large Asian kilns shared by several village potters describe several weeks of steady stoking per firing. | ||
==Kiln variants== | ==Kiln variants== | ||
One variant on the anagama style is the ''' |
One variant on the ''anagama'' style is the ''waritake'' kiln. A ''waritake'' kiln is akin to ''anagama'' in structure, but it has partition walls built every several meters through the length of the kiln. Each partition can be side stoked. | ||
A ''noborigama'' 登り窯 chambered climbing kiln is also built on a slope, and each succeeding chamber is situated higher than the one before it. The chambers in a noborigama are pierced at intervals with stoking ports. Such climbing kilns have been used in Japan since the 17th century. The largest working ''Noborigama'' kiln in Japan is located in ], in the southern portion of Shiga Prefecture. | |||
⚫ | The |
||
The ''renboshiki noborigama'' is a multi-chambered climbing kiln. There are many distinguishing characteristics between the ''noborigama'' and ''anagama'' style. For example, an ''anagama'' is somewhat like a half-tube (long ]) with a fire burned at the lower end. A ''noborigama'' is like a set of half-tubes (]es or short vaults, ]ing each other) placed side-by-side with piercings that allow each chamber to feed into the next. | |||
⚫ | The main advantage |
||
⚫ | The ''jagama'' (snake kiln or ]) is related to ''anagama'', ''noborigama'', and ''waritake'' kilns, and was used extensively in China since at least the 3rd century CE. ''Jagama'' are tube shaped similarly to ''anagama'' kilns, but can be longer at around 60 m. Although partitioned and side stoked, ''jagama'' do not have partition walls, rather, improvised walls are created by densely stacking pottery at intervals. | ||
⚫ | == References == | ||
⚫ | Furutani, Michio |
||
== Characteristics == | |||
⚫ | ==External |
||
⚫ | The main advantage of climbing kilns is that heat from the burning fuel is re-used, the same heat heating more than one part of the kiln. Exhaust heat created during firing of the lower part of the kiln, preheats the chambers above. In addition, the cooling ware and walls below preheat the incoming air. Thus, firing of ware in the upper chambers requires only the additional fuel needed to bring the ware, walls and air to peak temperature. (From a ] point of view, the higher temperature of combustion and cooler exhaust suggest greater efficiency.) A modern type, called a '']'' improves the efficiency and output still further by having the ware move through the kiln in a direction opposite to that of the hot gasses. | ||
* | |||
⚫ | * | ||
All of these kilns use two ''counter-flow exchange mechanisms'' to maintain the air supply and to change the ware being fired, with minimal loss of heat. Each of these exchanges works on the same principle as ], the principal difference being that the ware is not a fluid. | |||
An advantage of the chambered and semi-chambered variants appears to be that they are partly downdraft, which makes the firing results less sensitive to the way the ware is loaded. | |||
A disadvantage of smaller climbing kilns is a tendency to rapid cooling, caused by the incoming air. | |||
== See also == | |||
* ] | |||
⚫ | == References == | ||
{{reflist}} | |||
{{No footnotes|date=May 2009}} | |||
⚫ | * {{cite web |author=Furutani, Michio |title=Anagama: Building Kilns and Firing (2003) (unpublished translation manuscript on file with anagama-west.com |url=http://www.anagama-west.com/anagama/book/anagama_translation.php}} | ||
⚫ | ==External links== | ||
⚫ | ] | ||
* Cofield, Jay. "." ''Southern Spaces'', 10 June 2008. | |||
⚫ | * | ||
* | |||
* Carlson, Scott. ''Chronicle of Higher Education'', 13 February 2009. A story about a potter who built the Johanna Kiln, the largest wood-fired kiln in North America. | |||
] | |||
] | |||
⚫ | ] |
Latest revision as of 14:32, 30 June 2024
Ancient type of pottery kiln
1 Door about 75 centimetres (30 in) wide
2 Firebox
3 Stacking floor made of silica sand
4 Dampers
5 Flue
6 Chimney
7 Refractory arch


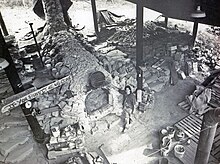
The anagama kiln (Japanese Kanji: 穴窯/ Hiragana: あながま) is an ancient type of pottery kiln brought to Japan from China via Korea in the 5th century. It is a version of the climbing dragon kiln of south China, whose further development was also copied, for example in breaking up the firing space into a series of chambers in the noborigama kiln.
An anagama (a Japanese term meaning "cave kiln") consists of a firing chamber with a firebox at one end and a flue at the other. Although the term "firebox" is used to describe the space for the fire, there is no physical structure separating the stoking space from the pottery space. The term anagama describes single-chamber kilns built in a sloping tunnel shape. In fact, ancient kilns were sometimes built by digging tunnels into banks of clay.
The anagama is fueled with firewood, in contrast to the electric or gas-fueled kilns commonly used by most modern potters. A continuous supply of fuel is needed for firing, as wood thrown into the hot kiln is consumed very rapidly. Stoking occurs round the clock until a variety of variables are achieved including the way the fired pots look inside the kiln, the temperatures reached and sustained, the amount of ash applied, the wetness of the walls and the pots, etc.
Burning wood not only produces heat of up to 1400°C (2,500 °F), it also produces fly ash and volatile salts. Wood ash settles on the pieces during the firing, and the complex interaction between flame, ash, and the minerals of the clay body forms a natural ash glaze. This glaze may show great variation in color, texture, and thickness, ranging from smooth and glossy to rough and sharp. The placement of pieces within the kiln distinctly affects the pottery's appearance, as pieces closer to the firebox may receive heavy coats of ash, or even be immersed in embers, while others deeper in the kiln may only be softly touched by ash effects. Other factors that depend on positioning include temperature and oxidation/reduction. Besides location in the kiln, (as with other fuel-fired updraft kilns) the way pieces are placed near each other affects the flame path, and, thus, the appearance of pieces within localized zones of the kiln can vary as well. It is said that loading an anagama kiln is the most difficult part of the firing. The potter must imagine the flame path as it rushes through the kiln, and use this sense to 'paint the pieces with fire'.
The length of the firing depends on the volume of the kiln and may take anywhere from 48 hours to 12 or more days. The kiln generally takes the same amount of time to cool down. Records of historic firings in large Asian kilns shared by several village potters describe several weeks of steady stoking per firing.
Kiln variants
One variant on the anagama style is the waritake kiln. A waritake kiln is akin to anagama in structure, but it has partition walls built every several meters through the length of the kiln. Each partition can be side stoked.
A noborigama 登り窯 chambered climbing kiln is also built on a slope, and each succeeding chamber is situated higher than the one before it. The chambers in a noborigama are pierced at intervals with stoking ports. Such climbing kilns have been used in Japan since the 17th century. The largest working Noborigama kiln in Japan is located in Shigaraki, in the southern portion of Shiga Prefecture.
The renboshiki noborigama is a multi-chambered climbing kiln. There are many distinguishing characteristics between the noborigama and anagama style. For example, an anagama is somewhat like a half-tube (long vault) with a fire burned at the lower end. A noborigama is like a set of half-tubes (arches or short vaults, buttressing each other) placed side-by-side with piercings that allow each chamber to feed into the next.
The jagama (snake kiln or dragon kiln) is related to anagama, noborigama, and waritake kilns, and was used extensively in China since at least the 3rd century CE. Jagama are tube shaped similarly to anagama kilns, but can be longer at around 60 m. Although partitioned and side stoked, jagama do not have partition walls, rather, improvised walls are created by densely stacking pottery at intervals.
Characteristics
The main advantage of climbing kilns is that heat from the burning fuel is re-used, the same heat heating more than one part of the kiln. Exhaust heat created during firing of the lower part of the kiln, preheats the chambers above. In addition, the cooling ware and walls below preheat the incoming air. Thus, firing of ware in the upper chambers requires only the additional fuel needed to bring the ware, walls and air to peak temperature. (From a thermodynamic point of view, the higher temperature of combustion and cooler exhaust suggest greater efficiency.) A modern type, called a tube kiln improves the efficiency and output still further by having the ware move through the kiln in a direction opposite to that of the hot gasses.
All of these kilns use two counter-flow exchange mechanisms to maintain the air supply and to change the ware being fired, with minimal loss of heat. Each of these exchanges works on the same principle as countercurrent exchange, the principal difference being that the ware is not a fluid.
An advantage of the chambered and semi-chambered variants appears to be that they are partly downdraft, which makes the firing results less sensitive to the way the ware is loaded.
A disadvantage of smaller climbing kilns is a tendency to rapid cooling, caused by the incoming air.
See also
References
![]() | This article includes a list of references, related reading, or external links, but its sources remain unclear because it lacks inline citations. Please help improve this article by introducing more precise citations. (May 2009) (Learn how and when to remove this message) |
- Furutani, Michio. "Anagama: Building Kilns and Firing (2003) (unpublished translation manuscript on file with anagama-west.com".
External links
- Cofield, Jay. "Montevallo's Anagama." Southern Spaces, 10 June 2008.
- The Log Book, the magazine about anagamas and woodfiring in general
- An anagama kiln built according to Furutani Michio's design principles, podcasts with woodfire potters, photogalleries of woodfired work
- Carlson, Scott. Earth, Wind, and Fire: Richard Bresnahan's elemental approach to art — and life Chronicle of Higher Education, 13 February 2009. A story about a potter who built the Johanna Kiln, the largest wood-fired kiln in North America.